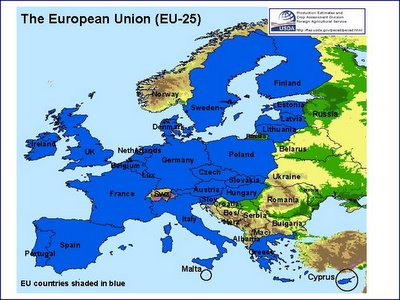
So, its time for a little look at European expansion...your company is global, and because it is no longer cost-effective to reach international customers from your U.S. operation, you need to open a European distribution center. Finding the best place to locate that hub is key.
The European Union is made up of 25 countries, all with their own laws and regulations, some of which are imposed on a European level. You also need to consider language barriers; unique employment, transportation, and warehouse rules; and directives from the European Economic Community.
Before making any decisions, you must carefully weigh a variety of factors, that will ultimately focus your decision. Here are some issues to contemplate:
1. Analyze your company's needs. The first step in the process is understanding your requirements. Be sure you can answer these questions: How much product is flowing and where is it flowing to? Where is the majority of your European customer base? What are your shipping needs? What products are you shipping -- medical, pharmaceutical, food, hazardous materials, garments, or fragile items?
2. Become familiar with the European Union's demographics and currencies. The original 15 EU countries have more mature economies than the 10 that joined in May of 2004. Bulgaria and Romania are in discussions to join the EU in 2007. Many of the original EU members use the euro, but not all. The United Kingdom and Sweden, for example, use their own currencies.
3. Check out national employment laws. Employment laws differ from country to country, which makes it challenging to manage your labor pool. This is especially so under the difficult trading conditions that exist in some countries, such as the employment protection and redundancy costs in France and Germany. Countries such as the UK, with more flexible laws, attract a greater number of companies. The cost of employing the staff also varies among countries, given different pension costs and vacation time, which makes a difference to your total labor amount. This employment information may be difficult to obtain.
4. Make sure you understand the country's planning laws. Building regulations change from country to country. In some nations, such as France, a different permit is required for storing chemicals, and new consent is required for storing metals or paper. In most other countries, general storage consent applies. In addition, modern DCs need 24- hour operation, but in some countries, facilities located near a residential area will have restrictions. The inability to operate 24 hours a day can substantially inhibit your business.
5. Learn the EU transport initiatives. The EU is working to get freight off roads and onto rail and water systems. It has a number of initiatives, such as Marco Polo, TEN-T and Motorways of the Sea, to encourage this idea. There is also a discussion about charging tolls (mainly in Germany, Belgium, and Holland). It is important to understand these initiatives and how they impact your business. Your decision should favor a location that offers different transportation modes and has access to ports.
6. Examine transport connectivity and infrastructure. Infrastructure is not consistent across Europe. Using rail transport, businesses face track gauge changes entering Spain and Russia as one challenge, but most national railroads still are comfortable in working their neighbors.. Consider how well your distribution center will link into the transportation system, specifically rail and water.
7. Know your potential exit strategies. You must understand the properties sale and leaseback value, and whether or not you will be able to exit the property if your circumstances change. Is the site attractive to another potential buyer? Issues such as remoteness, labor availability, specialization, and connectivity must all be examined. These factors affect the future sale or lease of the DC if you choose to move or leave the country.
8. Ask about available grant incentives. In certain economically disadvantaged regions, the government may encourage economic activity through grants, which boost financial investment in the country and its economy. These grants are definitely worth considering, but should not solely drive your location decision.
9. Understand the European drive time directives. Similar to the United States, the EU is reducing the number of hours truck drivers can work before taking a break, and putting limits on the number of hours a driver can work in one week. This substantially limits labor in the market and affects the number, size, and location of the distribution centers companies establish.
10. Check out property pricing and local taxes. Rents and investment yields differ across Europe to reflect market maturity. These dynamics change all the time. Countries have different ways of taxing property, which can impact your operations costs.
This is pretty strait forward advice. So, use it as a guide. Right now, the push to source and distribute product from some of the new EU countries is all the rage. The Czech Republic provides one of the best locations (in the heart of all European countries), matched with excellent labor talent and costs. Add the Czech Republic's robust transport infrastructure and you have well situated alternative to distribute your product into all of Europe. The Slovak Republic also presents an interesting alternative.
The bottom line is do your homework up front, and find people who know the market and understand the complexities to manage your foray into the EU market.